Unlock the Magic of FDM 3D Printing: Discover Its Secrets and Endless Possibilities!
FDM 3D printing, or Fused Deposition Modeling, has emerged as a transformative technology in the world of manufacturing. As industries strive for efficiency and innovation, FDM stands out as a reliable method that combines affordability with versatility. From prototyping to production, its relevance is undeniable, as it allows for the rapid creation of complex geometries that traditional manufacturing methods often struggle to achieve. With its growing popularity among hobbyists, educators, and professionals alike, FDM 3D printing is not just a trend; it's a revolution. I remember when a friend of mine first introduced me to FDM technology, showcasing how he created intricate models for his engineering projects. His enthusiasm was contagious, and it sparked my curiosity about the endless possibilities offered by this remarkable technology.
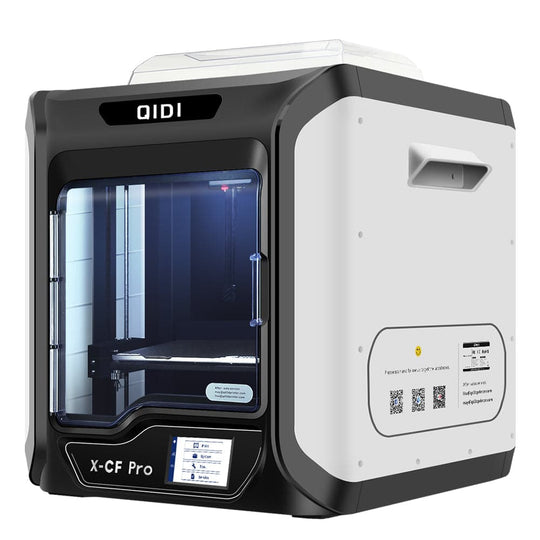
Understanding FDM 3D Printing
FDM, or Fused Deposition Modeling, is a 3D printing technology that builds objects layer by layer using thermoplastic materials. The process begins with a 3D model designed in CAD software, which is then sliced into thin horizontal layers. The FDM printer extrudes a thermoplastic filament through a heated nozzle, melting it and depositing it onto a build platform. The material cools and solidifies, forming a solid structure. This additive manufacturing technique is widely appreciated for its simplicity and effectiveness, making it accessible for both beginners and experienced users. The technology itself is based on the principle of material extrusion, where the filament is heated and pushed through the nozzle, allowing for precise control over the material deposition. The result is a highly customizable process that can produce intricate designs, making FDM a popular choice for diverse applications.
Principles of FDM Technology
The core principles of FDM technology revolve around material extrusion, layer adhesion, and the role of the 3D printer. Material extrusion is the heart of FDM, where the nozzle melts the filament and extrudes it onto the build platform. Layer adhesion is crucial; each layer must bond effectively with the one below to create a durable object. Factors such as temperature, speed, and material type play significant roles in achieving optimal layer adhesion. Moreover, the design of the 3D printer itself, including its movement mechanism and the heated build plate, greatly affects the printing process. For instance, the printer’s ability to maintain consistent temperatures can influence the quality of the final product. A friend who works in product design once shared his experience with FDM, emphasizing how mastering these principles transformed his prototypes from fragile models to robust, functional parts.
Applications of FDM 3D Printing
The applications of FDM 3D printing are vast and varied, spanning multiple industries. In aerospace, for instance, FDM is used to create lightweight components that can withstand extreme conditions while minimizing weight. The automotive industry leverages this technology for rapid prototyping, allowing for quicker iterations of designs and reducing time to market. In healthcare, FDM enables the production of personalized medical devices, such as prosthetics tailored to individual patients. Educational institutions have also recognized the value of FDM printing, using it as a tool for teaching engineering and design principles. I recall a local school hosting a 3D printing workshop where students used FDM technology to bring their creative ideas to life, showcasing how it fosters innovation and practical skills in young learners.
Advantages of FDM 3D Printing
FDM 3D printing offers a plethora of advantages that make it an attractive option for many users. One of the most significant benefits is its cost-effectiveness; the materials used are generally affordable, and the printers themselves can range from budget-friendly to high-end models. Additionally, FDM printing is known for its ease of use, making it accessible for beginners while still providing advanced features for experienced users. The versatility of materials is another key aspect; FDM can use various thermoplastics, including PLA, ABS, and PETG, each offering different properties suitable for specific applications. My friend, who is an avid 3D printing enthusiast, often highlights how the ability to experiment with different materials has expanded his creative horizons, allowing him to produce everything from functional tools to artistic sculptures. This blend of affordability, user-friendliness, and material diversity solidifies FDM's position as a leading method in the 3D printing landscape.
Embracing the Future of FDM 3D Printing
In conclusion, FDM 3D printing is a fascinating technology that has reshaped the landscape of manufacturing and design. By understanding its principles and exploring its applications, we can appreciate the advantages it offers across various industries. As we continue to witness advancements in 3D printing technology, the potential for innovation and creativity is limitless. Whether you're a hobbyist, educator, or professional, embracing FDM 3D printing can unlock a world of possibilities. So, why not dive deeper into this exciting field and see where your imagination can take you?