Unlocking the Future: Discover the Secrets of High-Precision SLS Printing!
In the rapidly evolving world of manufacturing and design, high-precision SLS (Selective Laser Sintering) printing has emerged as a game-changer. This innovative technology utilizes a laser to fuse powdered materials, layer by layer, into highly detailed and functional objects. As industries strive for greater efficiency and creativity, understanding the mechanics of SLS printing becomes essential. This article aims to delve into how high-precision SLS printing works, its diverse applications across various sectors, and the distinct advantages it holds over traditional manufacturing methods. Whether you are a designer, engineer, or simply a curious enthusiast, the insights provided here may inspire you to explore the possibilities of SLS printing.
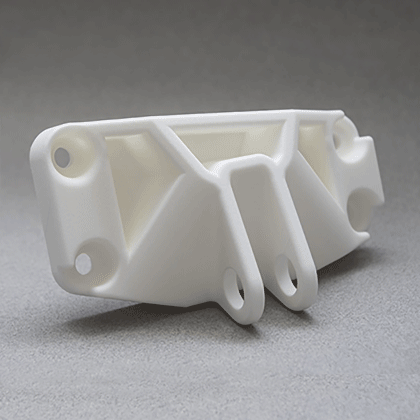
Understanding High-Precision SLS Printing
At the heart of high-precision SLS printing lies the principle of selective laser sintering. This process begins with a bed of powdered material—commonly nylon, but also including metals and composite materials—spread evenly across a build platform. A high-powered laser scans the surface, selectively fusing the powder particles together according to the digital model provided. Once a layer is completed, the platform lowers slightly, and a new layer of powder is applied, repeating the process until the object is fully formed. This layer-by-layer approach allows for intricate designs and complex geometries that traditional methods struggle to achieve.
Materials used in SLS printing are diverse, enabling a wide range of applications. From durable and flexible plastics to high-strength metals, the versatility of materials expands the potential for creating functional prototypes, end-use parts, and intricate designs. I remember a friend who works in automotive design sharing how they used SLS printing to create lightweight components that were not only strong but also tailored to specific performance needs. This capability to customize parts is a hallmark of SLS technology.
Applications of SLS Printing
The applications of high-precision SLS printing are vast and varied, impacting several key industries. In aerospace, for instance, SLS is utilized to produce lightweight, complex parts that meet stringent performance standards. The ability to create intricate geometries without additional tooling makes it ideal for rapid prototyping and small batch production.
In the automotive industry, SLS printing is revolutionizing how manufacturers approach design and production. Companies are using it to create everything from functional prototypes to final production parts, streamlining the development process. For instance, some automotive firms have created custom fittings and enclosures that are not only lightweight but also optimized for performance.
Healthcare is another sector reaping the benefits of SLS printing. Prosthetics and dental applications have been enhanced through the use of this technology, allowing for the creation of patient-specific devices that improve comfort and functionality. A friend of mine who works as a dental technician shared how SLS printing has enabled them to produce precise dental models that fit perfectly, reducing the need for adjustments and improving patient satisfaction.
Consumer products also benefit from SLS technology, enabling designers to experiment with innovative shapes and designs that were previously unfeasible with traditional manufacturing methods. The rapid turnaround and design flexibility offered by SLS mean that companies can respond quickly to market trends, creating products that resonate with consumers.
Advantages of High-Precision SLS Printing
The advantages of high-precision SLS printing over traditional manufacturing methods are significant. One of the most notable benefits is speed. The ability to produce complex parts in a single build process drastically reduces the lead time for prototypes and production runs. This speed can be a critical factor in industries where time-to-market is essential.
Design flexibility is another key advantage. SLS printing allows for intricate designs that would be impossible or prohibitively expensive to create using traditional techniques. This means that engineers and designers can push the boundaries of creativity without worrying about the limitations of manufacturing methods.
Material efficiency is also enhanced through SLS printing. Unlike subtractive manufacturing processes, which waste material by cutting away excess, SLS utilizes nearly all of the powder used in the build. Unfused powder can often be reused in subsequent prints, contributing to a more sustainable production process.
Moreover, SLS printing excels in creating complex geometries, such as internal channels or lattice structures that provide strength while minimizing weight. This capability has led to innovations in product design across many sectors. For instance, a friend who designs outdoor equipment highlighted how they used SLS to create a lightweight yet durable frame for a backpack, allowing for improved performance without compromising on strength.
Future Trends in SLS Printing
The future of high-precision SLS printing holds exciting prospects as technology continues to advance. Innovations in materials are on the horizon, with new powder formulations being developed to enhance performance, durability, and aesthetic qualities. These advancements may allow for even broader applications in various industries.
Machinery improvements are also expected, with new SLS printers offering faster build times, higher precision, and greater reliability. As competition in the 3D printing space increases, manufacturers are likely to invest in research and development to push the boundaries of what's possible with SLS technology.
Additionally, advancements in software and processing techniques will contribute to more efficient workflows, reducing the time and cost associated with preparing files for printing. The integration of artificial intelligence and machine learning could further optimize the printing process, identifying the most efficient ways to build complex designs. These trends indicate a promising future for high-precision SLS printing, solidifying its role as a key player in the manufacturing landscape.
Transforming Manufacturing with SLS Printing
In summary, high-precision SLS printing represents a significant shift in how we approach manufacturing and design. Its ability to create complex, customized parts quickly and efficiently makes it a valuable tool across various industries, from aerospace to healthcare. The advantages of speed, flexibility, and material efficiency set it apart from traditional methods, paving the way for innovative applications that were once thought impossible. As we look to the future, the potential advancements in SLS technology will undoubtedly continue to shape the landscape of manufacturing. For anyone involved in design or engineering, considering high-precision SLS printing could unlock new possibilities for your projects and inspire the next wave of innovation.