Unveiling the Secrets of SLS Prototyping: Transform Your Ideas into Reality!
In the ever-evolving world of product development, the need for rapid and efficient prototyping has become paramount. Enter SLS prototyping technology, or Selective Laser Sintering, a groundbreaking method that allows designers and engineers to turn their innovative ideas into tangible products quickly and accurately. This technology is not just a trend; it’s a game-changer in various industries, offering unmatched precision and flexibility. In this article, we will delve into the intricacies of SLS prototyping, exploring its functionality, diverse applications, and the future it holds for creators and manufacturers alike. Whether you're a seasoned professional or just starting your journey in product development, understanding SLS prototyping is essential for staying ahead in the competitive landscape.
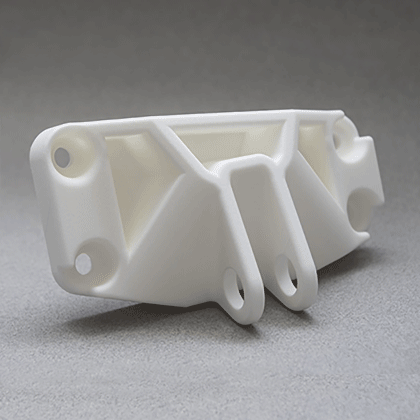
Understanding SLS Prototyping Technology
SLS, or Selective Laser Sintering, is an advanced 3D printing technology that utilizes a high-powered laser to fuse small particles of plastic, metal, ceramic, or glass powders into solid structures layer by layer. The process begins with a thin layer of powder spread across the build platform, followed by the laser tracing and sintering the material according to the digital design. The un-sintered powder acts as support for the model being created, which is one of the key advantages of SLS. This technique allows for the creation of complex geometries and intricate details that would be impossible with traditional manufacturing methods. Materials typically used in SLS include nylon, which is favored for its durability and flexibility, as well as other polymers that provide various mechanical properties tailored to specific applications.
How SLS Works
The SLS prototyping process involves several critical steps. First, the 3D model is designed using CAD software, which is then sliced into thin layers that instruct the printer on how to build the object. Once the design is finalized, a thin layer of powder is spread across the build platform. The laser then selectively sinters the powder according to the sliced design, melting and fusing the particles together. After the first layer is completed, the build platform lowers slightly, and a new layer of powder is applied. This process repeats until the entire model is completed. Once the printing is finished, the part is removed from the build chamber, and any excess powder is cleaned away, often requiring some post-processing to achieve the desired finish. This intricate layering and sintering technique not only enhances the model's strength but also opens up a world of design possibilities.
Applications of SLS Prototyping
SLS prototyping finds its applications across various industries, showcasing its versatility and effectiveness. In the automotive sector, for instance, SLS is used to create functional prototypes for testing and validation, allowing manufacturers to refine their designs before mass production. The aerospace industry benefits immensely from SLS's ability to produce lightweight yet durable parts that meet stringent regulations. Additionally, the healthcare sector utilizes SLS for custom medical devices, prosthetics, and even bioprinting applications, where tailored solutions are essential for patient care. These industries highlight the technology's capacity to not only enhance product development timelines but also improve the overall quality and performance of the final products.
Advantages in Rapid Prototyping
One of the standout benefits of SLS prototyping is its exceptional design flexibility. Unlike traditional manufacturing methods, SLS allows for complex geometries that can significantly reduce the number of parts in an assembly, leading to lighter and more efficient products. Moreover, the ability to work with a variety of materials enhances material efficiency, as designers can choose the most appropriate substance for their specific needs without being constrained by conventional manufacturing limitations. This rapid prototyping capability not only accelerates the product development process but also encourages innovation, as designers can quickly iterate and test multiple versions of their ideas without significant financial investment.
Challenges and Limitations of SLS Prototyping
While SLS prototyping offers numerous advantages, it is not without its challenges. One of the primary concerns is the initial investment required for SLS equipment, which can be substantial. Additionally, the process often necessitates post-processing steps such as sanding, polishing, or painting to achieve a smooth finish, which can add time and cost to the overall project. Another limitation is the potential for warping or deformation of parts during the cooling process, especially for larger models. These challenges can be mitigated through proper design considerations and process optimization, but they require careful attention from designers and engineers.
Future Trends in SLS Technology
The future of SLS technology looks promising, with emerging trends poised to enhance its capabilities further. Innovations in materials science are leading to the development of new high-performance powders that can withstand extreme conditions, broadening the scope of applications. Additionally, advancements in laser technology are paving the way for faster processing times and improved precision, making SLS even more appealing for rapid prototyping. The integration of artificial intelligence and machine learning in the design and manufacturing processes could also streamline workflows and enhance the efficiency of SLS prototyping, ultimately transforming how products are developed across various industries.
Harnessing the Power of SLS Prototyping
In summary, SLS prototyping technology is revolutionizing the way we approach product development, enabling designers and engineers to bring their ideas to life with unprecedented speed and accuracy. By understanding the principles of SLS, its diverse applications, and the challenges it presents, professionals can harness its potential to create innovative solutions in their respective fields. As technology continues to evolve, SLS prototyping is set to play an increasingly vital role in transforming concepts into reality, making it an invaluable tool for anyone involved in the product development process.